Des machines capables de produire rapidement des pièces de précision dans une diversité infinie de matériaux, du plastique le plus souple aux céramiques les plus résistantes, voilà ce que la PMI Pollen AM a inventé et fabrique avec son équipe, 100% à Ivry-sur-Seine. Portrait d’une entreprise pionnière avec Didier Fonta, son directeur général (photo).
Créée en septembre 2013 par Cédric Michel et Victor Roux, président de l’entreprise, Pollen AM a développé une technologie de fabrication additive (impression 3D) à dimension industrielle. Son premier défi fut ainsi d’utiliser de vrais matériaux, “c’est à dire pas des matériaux développés pour s’adapter à ce processus de fabrication, mais des matériaux déjà utilisés par les industriels”, détaille Didier Fonta, directeur général, qui a rejoint l’équipe en 2015 alors qu’elle était en phase de validation du produit.
Donner à l’impression 3D une vocation industrielle
Concrètement, il s’agissait de pouvoir utiliser des granulés plutôt que des filaments, de la poudre ou de la résine. Objectif : gagner en indépendance par rapport aux consommables des fournisseurs de machines et baisser les coûts pour que la fabrication additive ne soit pas réservée à du prototypage ou des pièces uniques, et puisse avoir une vocation véritablement industrielle. “C’était très novateur à l’époque. On est des véritables pionniers sur ce marché”.

Les premières expérimentations concernent alors les thermoplastiques, à la fois élastomères et rigides. Une première étape qui permet déjà toute une gamme de produits de toutes consistances. “C’est unique sur le marché de la fabrication additive. Les filaments et résines ne peuvent pas le faire”, reprend Didier Fonta.
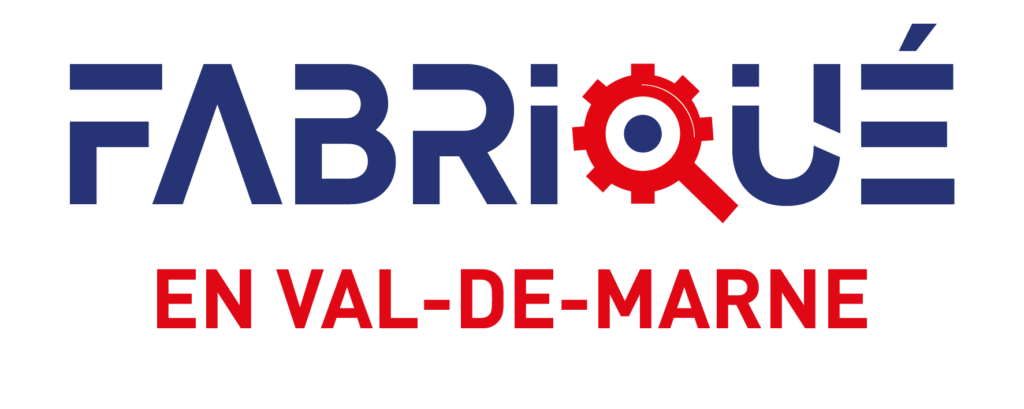
Cet article s’inscrit dans le cadre d’une série de portraits d’entreprise ambassadeurs du Fabriqué en Val-de-Marne réalisés avec le soutien de la Chambre de commerce et d’industrie, à l’initiative de ce programme. Plus d’informations sur l’initiative Fabriqué en Val-de-Marne
Du plastique au métal : première diversification
“On a lancé notre premier produit en juin 2016, sur VivaTech. On avait la chance d’être hébergé par deux grandes entreprises dont l’une était cliente. Nous y avons eu un très bon accueil du marché et cela nous a permis de rencontrer un grand groupe allemand qui nous a démarchés pour travailler sur le métal“, se souvient le directeur général.
Une sacrée diversification, opérée dans le cadre d’un partenariat avec le groupe d’outre-Rhin pour faire évoluer la technologie et les machines. “Nous avons lancé notre première gamme dédiée aux métaux en 2018.”

Là encore, les déclinaisons sont multiples, entre le cuivre, le tungstène… et encore les différentes formes d’acier. “On peut utiliser tous les métaux à partir du moment où on le trouve en poudre atomisée, c’est la seule limite.”
De VivaTech à FormNext : des salons qui dopent les opportunités
Fin 2018, la société travaille donc déjà les gammes plastiques et métaux, quand elle expose au salon de la fabrication additive Formnext en Allemagne. Nouvelle rencontre, cette fois avec un laboratoire belge, qui propose à Pollen de travailler les céramiques techniques.
“Celles-ci ont exactement le même fonctionnement que les métaux. Concrètement, on s’appuie sur un mélange de plastique et de poudre pour pouvoir former la pièce, puis on enlève le plastique et on consolide au four”, explique Didier Fonta. Le mélange des deux matériaux permet en effet de réaliser des formes qui ne pourrait se tenir dans le cadre de la fabrication additive, sans l’appui du plastique. Ce dernier peut s’enlever facilement ensuite, une fois la pièce formée.

“La céramique est un marché de niche mais a une très forte valeur ajoutée”
“On a rebrandé notre offre pour qu’elle corresponde aux métaux et aux céramiques techniques”, détaille le directeur. “La céramique est un marché de niche mais a une très forte valeur ajoutée.” Par rapport au métal, la céramique résiste en effet mieux aux fortes températures, c’est aussi un véritable isolant thermique et électrique. ”C’est notamment très utilisé dans le médical car c’est inerte.”
Transports, médical, sportswear…
Les machines, intégralement configurables, coûtent entre 30 000 et 80 000 euros, en fonction de la diversité de matériaux qu’elles peuvent traiter. Les clients sont les industriels qui fabriquent à partir de ces machines. Pollen ne fabrique pas directement de produits en série. Les principaux marchés : les transports, essentiellement l’aéronautique et les trains, le médical, la recherche, mais aussi les accessoires de sportswear comme par exemple les masques de plongée.
La clientèle, depuis le départ, fait une large place à l’export. “Plus de 80% de notre chiffre d’affaires est généré à l’international : en Europe, puisqu’on a la chance d’avoir une monnaie commune et un marché ouvert, mais aussi à Singapour, aux Philippines, au Japon, aux États-Unis… Au total, nous sommes dans 25 pays”, développe Didier Fonta.

100% fabriqué local
En termes de fabrication, l’intégralité du site de production est situé à Ivry-sur-Seine, où se trouve aussi le siège et un laboratoire de recherche et développement. “On a également une filiale en Belgique. Il s’agit d’une antenne de spécialisation dédiée aux travaux sur la céramique.” Une implantation destinée à se rapprocher du partenaire belge, BCRC (le laboratoire belge des céramiques). “Il a des équipements auxquels on n’aurait jamais pu avoir accès”, motive Didier Fonta.
Au total, Pollen emploie une dizaine de personnes, en comptant la production. Principale difficulté en termes de ressources humaines : le recrutement de commerciaux, en raison notamment de la technicité des produits, qui n’est pas non plus adaptée à une délégation des ventes à des agents ou distributeurs.

Progressivement, l’entreprise a délégué une partie de la préproduction. “Sur les premières machines, on faisait tout à partir des vis, tiges et éléments indépendants, parce qu’il fallait que l’on comprenne comment elles fonctionnent, et où étaient les problèmes de conception pour améliorer le procédé. Aujourd’hui, on achète des sous-ensembles mais 100% de notre production est française. Les seules choses qui ne sont pas faites en France, c’est lorsqu’il n’y a pas de savoir-faire français. C’est le cas de certains composants électroniques ou de moteurs. Mais même dans ce cas, notre carte électronique finale est faite en France.”
Le choix d’Ivry-sur-Seine a été motivé par la proximité immédiate de Paris mais aussi d’universités. “On a besoin d’attirer les talents. Or, ici, on est à côté d’universités comme Saclay. Il y a une attractivité territoriale qui est là.” Pour s’ancrer durablement toutefois, l’entreprise, actuellement en bail précaire, recherche 500 m2.
Face à la frilosité des investisseurs : s’appuyer sur ses clients
Une pépite d’innovation qui a néanmoins expérimenté les embûches de la croissance, à commencer par la frilosité des investisseurs. “La première fois que vous allez les voir, ils vous disent : ‘Super, vendez votre première machine.’ La deuxième, après avoir vendu, non pas une mais quarante machines, ils fixent un autre objectif, et ainsi de suite…, témoigne le directeur général. En attendant, on a décidé de compter sur nous-mêmes, avec nos moyens, en cherchant une rentabilité pour que ce soit le marché qui nous finance. Avec les risques que cela comporte, bien sûr.”
“Cadence de production et résolution”
Ce qui n’empêche pas la PMI de continuer à innover, alors que la concurrence se développe aussi. Dans les cartons : de nouvelles améliorations pour augmenter la productivité des machines et réduire les opérations humaines, afin de gagner en compétitivité par rapport aux pays à faible coût de main-d’œuvre. Un changement d’échelle qui passe aussi par la création de machines capables de travailler en parallèle. Sur le plan de la qualité, l’objectif est de faire disparaître les différences entre des pièces injectées ou réalisées en fabrication additive, comme les traits, caractéristiques du passage de chaque couche. Un double objectif résumé par le DG : “cadence de production et résolution.”
Lire aussi :
N'envoyez que des photos que vous avez prises vous-même, ou libres de tout droit. Les photos sont publiées sous votre responsabilité.