Des coques d’iPhone made in France, c’est possible, pas plus loin que dans le plateau briard, à Périgny-sur-Yerres. C’est l’une des nombreuses productions de Microplast, spécialiste de l’injection plastique : classique, bio ou recyclé. La PMI, qui fête ses 40 ans cette année, s’apprête à quasiment doubler de surface pour produire plus, de manière plus économe et écologique. Son secret depuis toujours : être à la fois mouleur et mouliste. Visite.
Avant Microplast, il y a d’abord eu la société Ecom, créée en 1978 pour étudier et fabriquer des moules. Microplast est créée en 1985, par les frères Lelard. D’abord basées à Crosnes et Saint-Maur-des-Fossés, les deux entités déménagement à Périgny-sur-Yerres en 2001. En 2004, Serge Lelard prépare sa succession en faisant monter deux de ses cadres au capital. David Anger est alors chef de la partie mécanique et Thierry Rouault de la partie plastique. “On a monté un LBO (Leverage buy out, montage financier permettant la reprise en recourant à l’endettement) sur sept ans, avec prêt personnel. À l’époque, on découvrait ce terme”, se souvient David Anger, président actuel (à droite sur la photo). Le fondateur ne sort définitivement de l’actionnariat qu’en 2018, occasion de faire entrer un troisième associé, Barthélémy Gagnon, actuel directeur général. “Mais le fondateur est resté impliqué, il vient régulièrement. On sent qu’il est fier de ce qu’est devenue la société.”
Du mono-produit mono-client au marché hyper diversifié
De fait, la PMI a parcouru un sacré bout de chemin en quarante ans. Au départ, elle ne fabriquait pourtant qu’un seul produit, des prises télécom RJ45, essentiellement pour un client, lequel a fini par se faire racheter puis a délocalisé sa production. Un coup dur pour la PMI qui se retrouve, au pied du mur, obligée de se diversifier à toute vitesse. D’autant que nous sommes alors en 2007 et que les nouveaux associés viennent de reprendre, avec leur prêt à rembourser. “On a recruté des commerciaux et on a fait preuve de créativité”, se souvient Jacques Doumeizel, directeur commercial et associé (à gauche sur la photo). La leçon a été retenue. “Aujourd’hui, Microplast couvre 8 marchés avec près de 200 clients.”
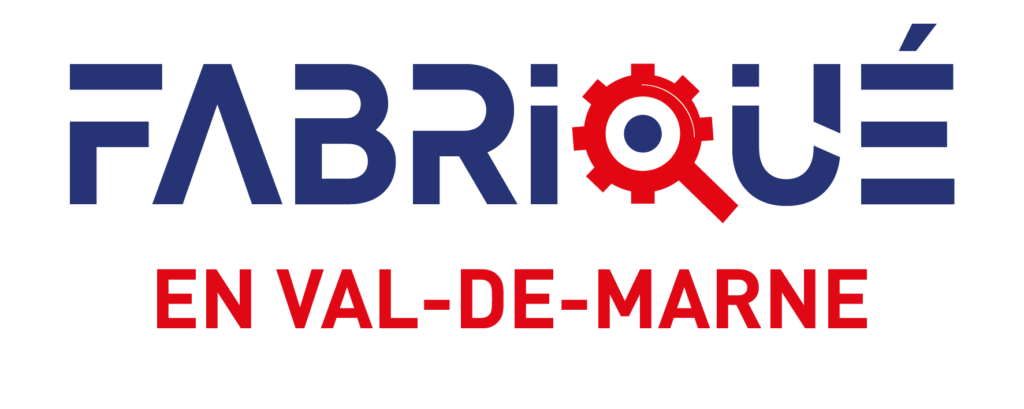
Cet article s’inscrit dans le cadre d’une série de portraits d’entreprise ambassadeurs du Fabriqué en Val-de-Marne réalisés avec le soutien de la Chambre de commerce et d’industrie, à l’initiative de ce programme. Plus d’informations sur l’initiative Fabriqué en Val-de-Marne
La matière première aussi s’est diversifiée, avec plus de 100 matières plastiques différentes. “Nous en avons à 2 euros le kilo, d’autres à plus de 100 euros. Nous travaillons avec des matériaux variés, allant du simple polypropylène aux matériaux techniques comme le Peek, thermoplastique haute performance, qui nécessite des moules chauffés à plus de 400 degrés”, détaille David Anger.
“La vraie force du groupe, c’est d’être mouleur-mouliste”
Des presses de Périgny-sur-Yerres, sortent désormais des coques de téléphone, de la connectique automobile, de la domotique (télécommande), de la robinetterie, des gourdes, des équipements pour le contrôle d’accès, des pièces pour le nucléaire, du jeu, de la machinerie agricole, du matériel pour le secteur médical (filtre seringue)… “On est capable de faire des pièces de 0,5 g à des pièces de 1,6 kg.”
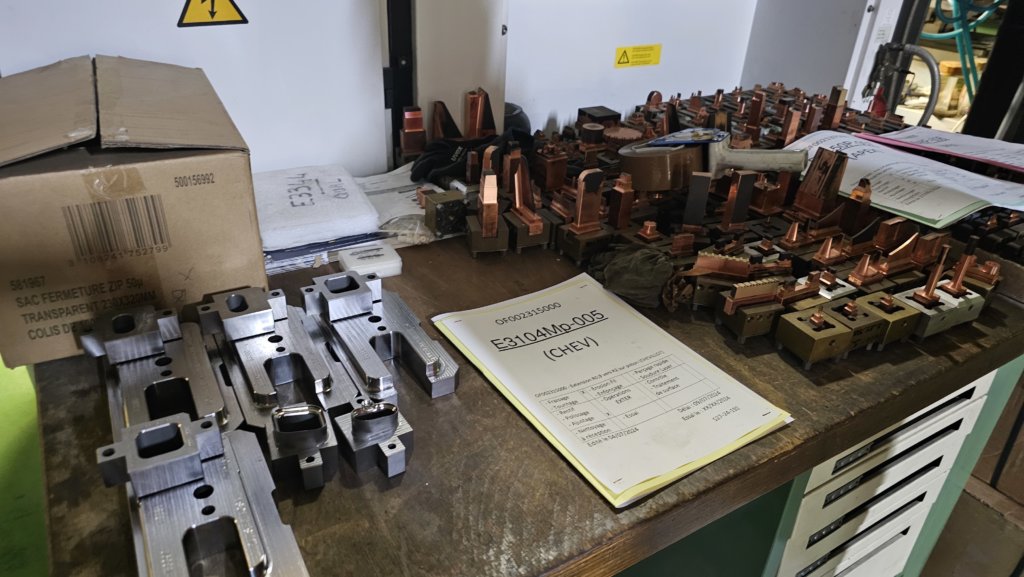
“La vraie force du groupe, c’est d’être mouleur-mouliste. Lorsque le client vient avec une idée, on va être capable de concevoir le produit, de le développer, de dessiner le moule, de le fabriquer et d’injecter le produit fini”, développe le président. La société n’a pas hésité à faire de la croissance externe pour disposer de toutes les compétences. “On fait tout de A à Z. Par exemple, la coque de téléphone, on la livre dans son packaging. Le client la reçoit prête à être mise en rayon.”
Le made in France : “un tout petit peu plus cher”
Des coques de téléphone made in France ? Cela peut paraître surprenant, étant donné la concurrence de pays comme la Chine. “On est un tout petit plus cher, mais il y a peu de différence, quand on tient compte des coûts de transport. Aujourd’hui, le made in France a le vent en poupe, les clients aiment voir l’étiquette bleu-blanc-rouge, même s’ils paient 1 ou 2 euros de plus. Et puis, cela fait une belle note RSE pour le donneur d’ordre.”
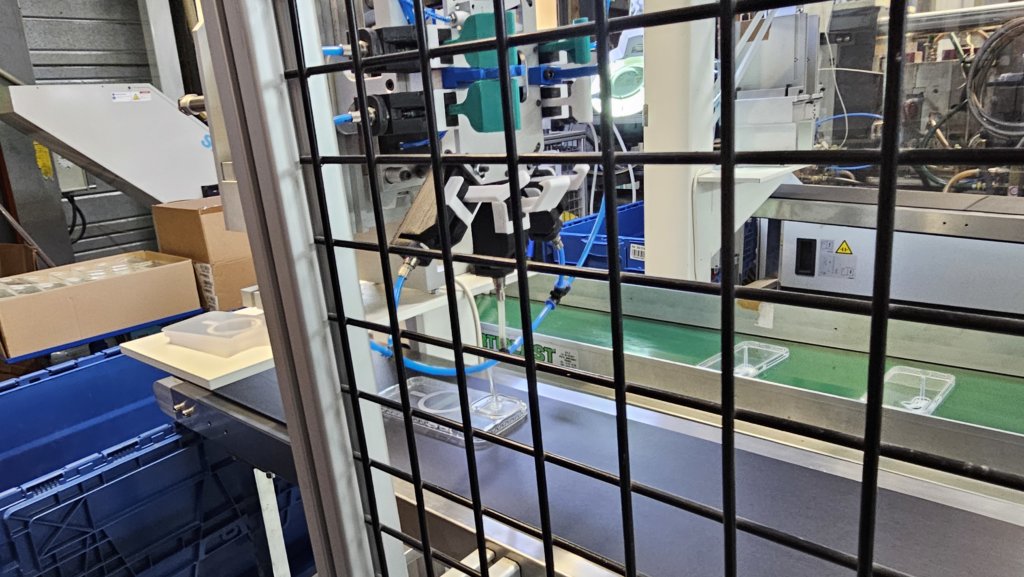
Le bioplastique : une alternative qui attend sa filière
Sur le plan écologique, Microplast teste les matières biosourcées, comme les fibres de bois, de maïs, de Miscanthus, la coquille d’huitre, de Saint-Jacques… même si cela reste marginal pour l’instant. “Aujourd’hui, les coûts sont très élevés sur ces matériaux, car les filières ne sont pas développées et les marchés ne sont pas mûrs.” Et puis, attention aux produits bio dans les voitures, prévient Jacques Doumeizel. Les nuisibles adorent !
Développer le plastique recyclé
La matière première reste donc essentiellement le plastique. “Pour des pièces techniques comme les connecteurs de voiture, le plastique restera indispensable”, insiste David Anger. “Par exemple, nous fabriquons des pièces plastiques pour l’automobile qui facilitent le traitement de surface et la mise en peinture des carrosseries. Celles-ci sont bien plus respectueuses de l’environnement que les anciennes pièces en métal, qui nécessitaient des décapages et consommaient beaucoup d’eau et d’énergie. Nos pièces plastiques sont réutilisables plusieurs fois et entièrement recyclables”, insiste Jacques Doumeizel.
À défaut de se passer de plastique, Microplast développe des filières de plastique recyclé, récupérant, par exemple, du plastique de phares de voitures pour créer des blocs de secours au-dessus des portes.
Parmi les prochaines innovations, la PMI envisage également de créer des dalles composées de matières recyclées au cœur, tout en conservant un matériau noble en surface pour les propriétés esthétiques, pour proposer une alternative aux dalles importées de Chine. “Ces dalles pourront être utilisées dans les bâtiments aux contraintes aérostatiques imposées, comme les hôpitaux, les usines, les collectifs, et permettront de valoriser des matériaux recyclés.” Une innovation dont la preuve de concept a été réalisée à l’occasion de l’agrandissement de l’usine pérignonne. “Nous avons fait nos propres moules. Comme cela, au lieu d’acheter 5 000 m² de dalles, on va les fabriquer nous-mêmes !”
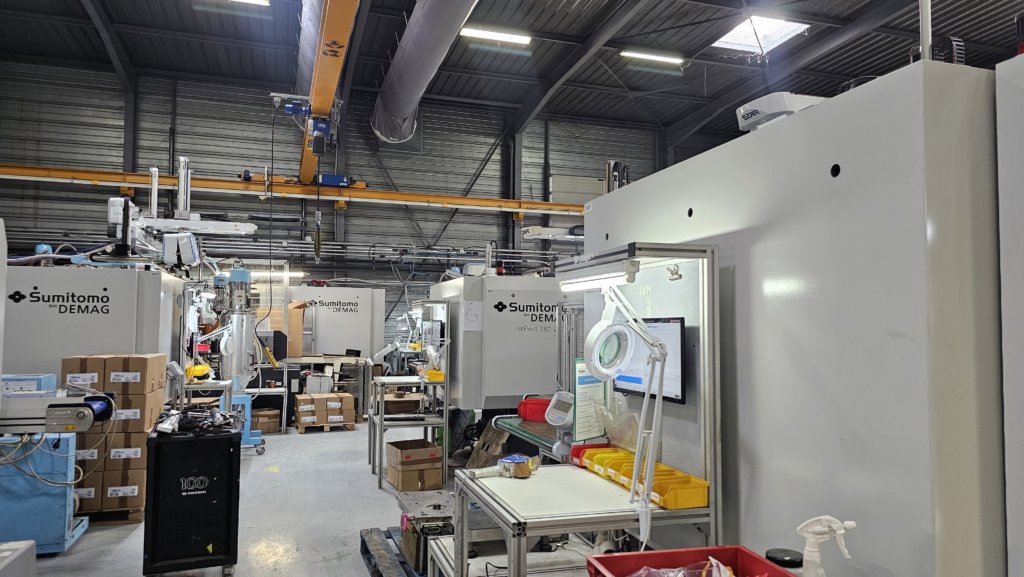
Extension, robotisation et réorganisation de la chaine pour éviter les discontinuités
En cours d’achèvement de travaux, l’extension de l’usine la fera passer de 3200 m2 à 5500 m2. L’occasion d’accueillir des robots six axes et de presses électriques très récentes. “Les presses électriques sont beaucoup moins énergivores et nous travaillons sur de nouvelles technologies pour gérer la matière (dessication, mise en température, retrait des poussières…) en réduisant de plus de 70 % la consommation énergétique”, développe Jacques Doumeizel. Un enjeu économique et écologique, car la gestion de la matière représente un tiers de la consommation Cela permettra de récupérer la matière pour la réinjecter.
L’extension vise aussi à réorganiser les machines en fonction du parcours des pièces. “L’espace permettra de positionner des îlots robotisés en périphérie des presses, ce qui est impossible à cause de l’exiguïté des locaux”, explique Jacques Doumeizel. “On va automatiser avec des caméras, des robots à six axes et du process. L’idée, c’est que la pièce injectée sorte de l’unité d’injection terminée, alors qu’actuellement, on a plein de petits postes à différents endroits pour faire des reprises. Désormais, une pièce sera injectée, tampographiée, soudée par ultrasons, emballée en chaîne”, illustre David Anger. “Il y a une discontinuité aujourd’hui dans la production. On ouvre et referme des cartons à longueur de journée.”
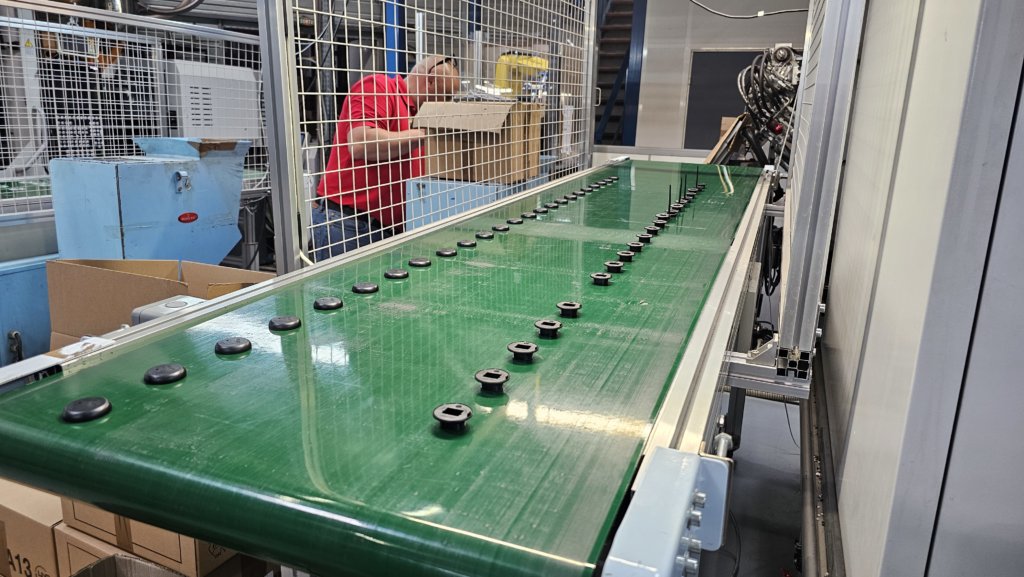
Évolution des profils
Objectif : minimiser les flux, mais, aussi, réduire la pénibilité, car il y aura beaucoup moins de manipulation. Ce seront les robots qui mettront les pièces dans les cartons. Il y aura en revanche plus de contrôle. Cela augmentera la capacité de production en tournant longtemps et de manière automatique, sans augmenter le nombre de presses, détaillent les dirigeants.
En termes de ressources humaines, cette mutation des process correspond à une transformation des profils des collaborateurs. “Les personnes peu qualifiées qui travaillent au pied des presses et qui partent en retraite sont remplacées par des techniciens supérieurs avec des compétences en automatisme, en robotique, en traitement d’images ou encore en traitement de données. Ce sont ces compétences dont on a besoin aujourd’hui pour aller vers une usine plus automatisée, plus robotisée, dans une logique d’Industrie 4.0”, détaille Jacques Doumeizel.
Du photovoltaïque pour couvrir la moitié de la consommation d’énergie
Au passage, l’entreprise va installer 3500 m2 de panneaux photovoltaïques sur le toit. “Cela couvrira 45 à 50 % de la consommation électrique.” À la clef, des économies qui devraient permettre d’amortir cet investissement énergétique sur sept ans. “En toute logique, on devrait se retrouver avec un coût par kilowatt autour de 0,18 – 0,19 euros, une fois qu’on sera en situation d’autoconsommation.”
Cap sur les quarante prochaines années
Quadragénaire depuis janvier, Microplast entend se donner les moyens de poursuivre son développement. “Nous suivons actuellement un programme accélérateur avec le Cetim et la BPI”, indique David Anger. La PMI joue aussi l’ancrage local, membre du Club d’entreprise du plateau briard et ambassadrice du Fabriqué en Val-de-Marne, initiative lancée par la Chambre de commerce pour valoriser les savoir-faire productifs. Parmi les axes de développement envisagés, la société n’exclut pas non plus de co-investir avec ses clients. “Aujourd’hui, explique ainsi David Anger, notre assise financière nous permet d’accompagner un client sur un produit auquel on croît.”
Microplast en bref
Effectif : 55 salariés
Création : 1985
Chiffre d’affaires : 17 millions d’euros
Clients : près de 200
Lire aussi :
N'envoyez que des photos que vous avez prises vous-même, ou libres de tout droit. Les photos sont publiées sous votre responsabilité.